Aircraft MRO Made Smarter: Minimize Aircraft on Ground Time, Maximize Efficiency
Table of Contents
Every unnecessary minute that one of your aircraft spends on the ground means:
- Lost profit and higher costs.
- Delays and cancellations across your fleet.
- The potential for negative passenger experiences.
That’s why your maintenance, repair and overhaul (MRO) operations are so vital.
But you already know that. You’re here because you want to make your MRO processes more efficient and reduce aircraft on ground time (AOG).
In this guide, we’ll show you how you can speed up data capture, improve supply chain visibility, and boost compliance and maintenance efficiency.
MRO inefficiencies: what’s the true cost?
Aircraft maintenance and repair is expensive.
In 2022, airlines worldwide spent $83.34 billion on MRO, representing about 10.9% of total airline operational costs.
Source: IATA
A study by Airline Economics found that AOG events cost the global airline industry an estimated $50 billion annually. And according to IAG Cargo Magazine, a grounded aircraft can cost an airline up to $150,000 per hour.
When you add inefficiencies into the mix, it’s easy to see how this can become a financial blackhole for airlines and air travel operators.
Despite the eye-watering costs associated with aviation repair and maintenance, the industry continues to suffer from inefficient documentation and data entry, and optimizing the MRO process across the entire supply chain:
- Research suggests that engineers and technicians spend up to 50% of their time completing paperwork and various compliance activities rather than working on aircraft.
- Paper-based documentation is still common, with two-thirds of airlines actively working to reduce paper usage.
- Even those using digital documentation can still find themselves hamstrung by laborious tasks like manual data entry. Entering long serial numbers or ordering parts by manufacturing numbers can be time-consuming and error-prone.
- The industry is plagued by supply chain visibility issues. U.S. passenger airlines reported a cost of $101.18 per block minute due to delays caused by supply chain inefficiencies.
- The global aircraft fleet is aging, having risen to 14.8 years, up from 13.6 years in earlier decades. Older aircraft of course require more maintenance, increasing demand for MRO services.
of aerospace and defense companies experience disruptions due to supply chain visibility gaps, costing an average of $184 million annually per company.
Source: Gartner
This presents a clear need for airlines to ensure efficient MRO operations to keep their fleet airworthy.
The solution? Smarter, more efficient MRO.
Airlines can drastically cut costs, downtime, and inefficiencies by leveraging smart data capture, AI, and computer vision to modernize MRO operations, and increase accuracy and visibility.
How intelligent data capture revolutionizes MRO operations
Scandit helps airlines to streamline their MRO operations with smart data capture on camera-enabled mobile devices, tablets, handheld computers, and wearable tech.
Our software enables smart devices to deliver real-time actionable insights and automate workflows by capturing barcodes, text, and objects via the device’s camera.
This removes the need for manual data entry, making MRO tasks quicker, more accurate, and more efficient. It also helps towards sustainability goals by removing the need for paper-based task cards and documentation.
Here’s how that can revolutionize your maintenance and repair workflows:
- Scan parts in and out of the aircraft during repairs to ensure visibility.
- Provide digitally documented proof of completion when a job is done.
- Track tools and equipment so technicians can see when and where they were last used, and by whom.
- Speed up warehouse tasks like receiving, counting, picking and stocktaking.
- Quickly reorder and return parts and equipment with a simple scan.
Let’s take a closer look…
Fast, reliable barcode scanning for better maintenance documentation
For more compliant and transparent MRO processes, accurate documentation is key. This can be digitalized and sped up with scanning technology to help keep a log of activity.
Ergonomic scanning for any workflow
SparkScan is a high-performance, ergonomic scanning solution that instantly transforms any smart device into an efficient barcode scanner. Designed for speed and ease of use, it enables seamless, high-volume scanning with minimal effort – perfect for maintenance teams handling aircraft parts, tools, and equipment.
Using SparkScan, staff can scan parts in and out of the aircraft during maintenance jobs. They can also scan specialist tools and equipment to ensure visibility of where they are and when they were used.
Once a job is finished, a quick scan of the parts can help to provide a digital proof of completion, with real-time updates sent to your centralized MRO systems.
Low- and no-code integration into your apps and systems
SparkScan can be integrated with your existing systems, meaning the data captured from each scan is seamlessly brought into your service application, whether it’s a native or web-based application.
If your app cannot be modified, or you need to deploy scanning capability quickly, Scandit Express is a no-code solution that floats on top of your application and provides enterprise-grade barcode scanning, injecting the captured data into your system.
High-performance scanning in the toughest conditions
Of course, MRO technicians often work in tough environments and conditions, which can make scanning difficult. With Scandit, this is no problem, as the software can scan in even the most challenging of circumstances:
- Scan in low light, glare, dusty or dirty surroundings, and inclement weather.
- Scan from long distances and at awkward angles.
- Scan damaged or tiny barcodes – even those etched onto metal parts and equipment.
- Preserve device battery life for up to 20% longer, helping to keep technicians connected in the field.
- Works on a range of devices from ruggedized smartphones to rugged handheld computers.
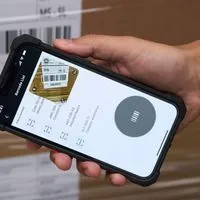
Try a scanning demo
Run a demo of SparkScan in your browser or on your smartphone now.
AR-guided instructions and installation support
Engineers can further reduce the need for paperwork thanks to augmented reality (AR) guidance during the job. By scanning parts, they can access AR overlays which provide installation instructions on the device screen.
Streamlined supply chain visibility and inventory management optimization
To prepare for jobs, technicians must conduct inventory checks on parts and tools, both in maintenance depots and service vehicles. This process is often time-consuming and prone to counting errors.
With MatrixScan Count, technicians can dramatically accelerate inventory counts and receiving of shipments, ensuring greater accuracy and efficiency. The AR overlays indicate which items on a pallet or shelf have been scanned, removing the guesswork.
- 10x faster receiving and inventory counting workflows
- The ability to capture multiple part barcodes in a single scan, reducing manual effort
- Streamlined stock management, minimizing delays in critical maintenance tasks.
Scandit’s Smart Scan Intention feature leverages AI-powered algorithms to precisely identify and capture the correct barcode, even in complex environments where multiple barcodes are visible or aiming is less than perfect.
Smart Scan Intention takes into account information related to the environment, the barcodes, different characteristics, but also the movement of the user to define and analyze which barcode they intend to scan. Even when aiming is imperfect it still manages to understand the right barcode.
Anne-Marie de Weijer, Product Marketing Manager, Scandit
For airline MRO operations, this capability significantly enhances efficiency in parts tracking, inventory management, and maintenance workflows, delivering benefits such as:
- Up to 100% elimination of incorrect scans, reducing errors in critical component tracking.
- Faster part identification and retrieval, accelerating maintenance turnaround times.
- A smoother user experience by minimizing rescans and manual data entry, ensuring technicians can focus on essential tasks.
See it in action with this side-by-side comparison:
When it comes to finding parts in a warehouse or service vehicle, MatrixScan Find provides intuitive AR-guided search and find capabilities. Technicians simply scan the entire shelf, and the AR overlay indicates the item to be picked.
Reordering processes can also be optimized to prevent stockouts. Rather than calling workshops and relaying long barcode numbers, or manually entering parts into a website, a quick barcode scan can drastically reduce the time taken to reorder and return parts.
The results?
- Enhanced accuracy in tracking maintenance schedules.
- Reduced risk of regulatory non-compliance due to errors or delays.
- Streamlined tracking of serialized components across the aircraft lifecycle.
It’s easy to implement and integrate with your MRO systems
Scandit Smart Data Capture technology is designed for effortless integration with existing ERP and MRO platforms, ensuring a smooth transition without disrupting current workflows.
The software enables smart device-based scanning, allowing you to leverage smartphones, tablets, handheld computers and wearables for MRO tasks. It can be integrated into any Android or iOS native app, as well as web-based applications.
From regional carriers to global airlines, Scandit’s technology scales effortlessly to meet the needs of any operation. Whether you’re managing a small fleet or an extensive network of maintenance hubs, Scandit provides consistent, high-performance scanning to streamline workflows across all locations.
Scandit ensures a smooth onboarding process and ongoing customer support meaning you can confidently deploy and maintain the solution for long-term success.
Clear for take-off: upgrade MRO workflows and reduce AOG time
Minimizing aircraft on ground time is critical to maintaining your airline’s profitability, operational efficiency, and passenger satisfaction.
To achieve this, efficient MRO operations are essential. Updating your technology can empower technicians with real-time data, seamless barcode scanning, and automated workflows, allowing you to improve on the metrics that matter: reduced downtime, increased data accuracy, and cost savings.
The Scandit technology helps to power the maintenance operations of leading global airlines.
Ready to revolutionize your MRO? Start a free trial today to see how Scandit can help you maximize efficiency and minimize AOG time.
Try Scandit today
Streamline MRO operations with smart data capture. Start your 30-day free trial.