Fast-Track Field Technician Efficiency with a Smart Device Assistant
Table of Contents
Field technicians often come up against operational issues and process inefficiencies. These range from delays while searching for parts or loading vans, to being poorly equipped with the tools and information needed to resolve issues.
You can change that by supercharging your technicians’ daily operations. Empower them with a high-performance, smart data capture-enabled device, to track and commission assets quickly, efficiently, and accurately.
This guide details how a smart device first approach will:
- Give your staff smart guidance to get field operations tasks right the first time.
- Ensure your technicians spend less time searching for parts and more time getting the job done.
- Increase customer satisfaction with first time fix rates.
Automate field operations for real-time visibility
Field service technicians are skilled professionals with packed daily schedules delivering installation, maintenance and repairs to physical infrastructure that businesses and consumers rely on everyday.
They work on critical assets in a wide range of industries including network infrastructure, telecoms, grid networks, HVAC, security systems, water treatment works, pest control, and more.
While the sectors are diverse, there are a number of shared operational challenges. A factor central to success is workforce management – assigning the right technician to the right job at the right time. Operational errors can play havoc with customer relationships, cause reputational damage and ruin business revenues.
A surprising percentage of field service businesses depend on outdated practices or manual methods such as whiteboards, Google Docs or a phone tag to manage inventory, dispatch technicians and complete tasks. Yet, many of these processes can be automated with barcode scanning, to reduce dependencies on manual methods and eliminate errors.
increase in field operation productivity for businesses that automate and digitize processes.
Source: McKinsey
Smart data capture enables any smart device to interact with physical items by capturing data from barcodes, text, IDs and objects with unmatched speed, accuracy and intelligence. This can power existing asset tracking and scheduling native apps or web applications to help modernize field operations.
Call time on time-consuming inventory counts
In readiness for their workday, technicians deliver inventory counts of parts and tools, both at the depot, and in the van. This time-consuming, labor-intensive process is prone to counting errors.
With technologies such as MatrixScan on smart devices, technicians significantly speed up inventory counts.
faster receiving and inventory counting workflows with MatrixScan, helping technicians to accurately capture multiple parts barcodes in a single scan – making stock counting easy.
Scandit’s Smart Scan Intention feature uses AI-powered algorithms to accurately detect and capture the desired barcode, even when aiming is imperfect or multiple barcodes are in the field of view.
This can dramatically improve efficiency in inventory counting and picking and receiving workflows, with results like:
- Up to 100% reduction in unwanted scans.
- Double picking speed.
- Improved user experience by reducing frustration caused by rescans and manual corrections.
See Smart Scan Intention in action here, with this side-by-side comparison of the feature switched off and on:
Many electrical components and parts, such as routers, come with multiple barcodes and numbers on one label. With Smart Label Capture, technicians can capture all the data they need from the labels with a single scan, making data entry up to seven times faster.
Field technicians who make their mobile inventory traceable in real-time by scanning parts:
- Provide real-time visibility of stock to all teams.
- Enhance job allocation based on parts availability.
- Eliminate repeat site visits owing to missing parts.
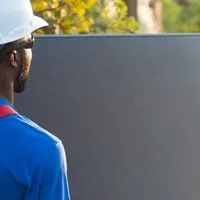
Case study
SunPower technicians reduce time to commission solar systems from 60 to 20 minutes with MatrixScan.
Take stock of parts with high-performance smart device scanning
Whilst a first-time fix is key to success, one of the main reasons for secondary visits is that technicians don’t have the appropriate parts available to resolve customer issues.
Service work orders are ideally planned with all the necessary parts in place. Sometimes though, field technicians will diagnose issues onsite, but lack the parts required to complete the repairs.
of service organizations have increased focus on service parts management due to growing customer demand for prompt resolutions of service issues.
Source: Aberdeen Research
Technicians using manual processes will typically call their warehouse with the serial number from the malfunctioning part, to check whether it’s in stock. Alternatively, if they use a website to reorder parts, field technicians must type in complex codes, sometimes up to 14 digits long, a potentially error-prone process.
Instead, they can use their smart device and scan-to-reorder, turning an inconvenience into a task that takes seconds.
Streamline ‘search and find’ for fast, first-time fixes
Finding the right part can be time-consuming. With a simple scan, field technicians and anyone involved in field operation workflows can search and find parts, tools and equipment instantly.
Gain access to customer data
Augmented reality overlays can reveal service history, future maintenance schedules, and details about parts that need replacing. Scanning of existing parts makes it easier to track and trace fitted parts under warranty for claims.
With this end-to-end visibility of parts that are in stock, field operations can be planned for first-time fixes, as:
- Parts are recorded and picked in advance of each visit.
- Faster finding of parts saves significant time across multiple work orders.
- Costs associated with unnecessary parts purchase are eliminated.
Lower operational costs, tracking inventory and resources
Smart scanning enables parts and equipment tracking from receipt to deployment, improving efficiency, preventing unauthorized stock use, and reducing operational costs.
This is helpful in a number of ways:
- Streamline job scheduling with shared inventory: By enabling automation of daily operational workflows, dispatchers can accurately match field technicians to a work order. Parameters could be based on available inventory proximity between the technician’s and customer’s location, and more. This maximizes inventory and personnel utilization, minimizes asset allocation errors, and mismatched resources.
- Just-in-time stock ordering: Better parts tracking means that parts are reordered only when needed, just-in-time. This prevents overstocking and understocking of parts, which keeps operational costs down and liquidity high.
- Warranty activations, claims processing and product recalls: With unified access to all service applications and resources on their devices, field technicians can make informed decisions – such as seamlessly activating warranties when commissioning systems; providing accurate diagnosis and repairs for warranty claims; and ensuring prompt recalls of defective parts.
Get actionable information with AR
Scandit’s augmented reality (AR) features make field operations intuitive for diverse daily activities, on the road, and onsite.
With a simple scan powered by AR overlays, technicians gain immediate access to a wealth of real-time information about the customer, the equipment and parts needed to complete tasks for first-time fixes.
See how augmented reality works to make workflows more efficient in the field:
- Upsell opportunities with actionable information: Warranty expiry and service term end notifications on the technician’s smartphone or handheld computer present revenue potential for upsell of additional parts and services to customers.
- Minimize rigorous technician training with connected technologies: Whether it’s experienced technicians or novice contractors, enabling them to install or fix equipment onsite is made easy with instant access to AR overlay based manuals, schematics, and installation instruction prompts. Thereby reducing the need for training, which is also helpful when onboarding new technicians to ramp up activity.
- Learning and development opportunities: Younger technician trainees who are digitally-savvy can also connect with seasoned professionals in real-time to help facilitate learning and have their questions answered. AR based remote, on-demand training serves as a smart tool to bridge the skills gap and attract younger talent to an industry beset by an aging workforce with not many takers.
- Improve customer satisfaction with proof of completion: Technicians can mark jobs complete by using AR to fill in service reports, add photos and external documents to jobs, capture IDs on equipment, and customer signatures. They can also automatically generate invoices and collect payments onsite with a smart device based mPOS connected to an ERP system for processing payments.
Integrate with ease for flexibility
High-performance scanning is a critical success factor in boosting performance in the field. Poor user experience can negatively impact your field technicians’ efficiency.
For instance, inaccuracies in barcode scanning for parts tracking will prevent technicians from gaining a clear view of stock availability, which may necessitate a secondary visit to a dissatisfied customer.
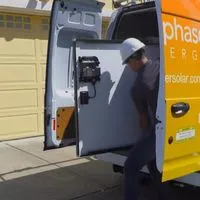
Case study
Discover how 100% scanning accuracy with real-time verification reduced install visits for Enphase Energy field technicians.
Therefore, it’s important that field technicians are equipped with high-performance smart data capture solutions such as those offered by Scandit that scan barcodes accurately in any condition including low light, glare, seasonal vagaries, varying distances, awkward angles, and on damaged barcodes. It can even scan tiny barcodes.
- High compatibility across devices and operating systems: 20,000+ smartphone and handheld computer models are compatible with Scandit’s barcode scanning SDK, which scans any barcode type.
- Start scanning quickly: SparkScan, our flagship barcode scanning solution, is a low-code, pre-built component that means you can quickly add enterprise-level barcode scanning to any existing application. The SparkScan shutter button and camera preview layer floats on top of your existing interface, and colors, sizes, and positions of elements can be easily customized to fit your app’s existing user interface.
- Third-party integrations: It’s important to consider integration requirements early on, when planning the right scanning solution. For instance, are there field service management apps, scheduling systems, or other backend solutions that the scanning solution will need to integrate with? Scandit can advise on the best approach.
Instant scanning to power field operations
Track parts and inventory instantly, eliminate integration efforts altogether for fast and easy technology deployment with the no-code Scandit Express. Add market-leading barcode scanning quickly to any existing infrastructure and legacy apps.
Scandit Express is ideal if you need to deploy a solution very quickly, cannot modify existing applications, or have limited or non-existent engineering resources.
Our service technicians love using Scandit Express. We’ve achieved improved scanning accuracy in all conditions and made our service calls shorter.Brian Golden, Vice President – Field Operations, Altafiber
All set to power field technician productivity with a smart data capture enabled smart device pocket assistant?
Talk to us about how you can give technicians instant access to the information they need to deliver superior customer service.
Give your field technicians the technology they deserve
Try Scandit for free, with a 30-day trial, and see how it helps your field techs become more efficient.